The Best Seat in the House: Navigating Theatre Seating Options for Maximum Enjoyment
When attending a theater performance, the quest for the best seat is a pursuit of optimal enjoyment. The location inside the venue can greatly influence the overall experience, impacting visibility, immersion, and comfort. Navigating through the various seat options requires careful consideration and understanding of the layout, sightlines, and personal preferences. By making informed choices, theatergoers can secure the best seat in the house and ensure a truly memorable and immersive experience.
19″, 20″, 21″, 22″, 23″, 24″, some vary for on models and configurations.
Typical row spacing can start at 32″ and go up.
Floor mount, flat or tiered, riser mount, telescopic, movable ganged in sets of 3 or 4, straight row or radius, Single unit movable.
Seat construction
Seating must be constructed in accordance with ASTM certified assembly process, under ISO 9001 guidelines, fabricator must demonstrate QC and testing processes and management.
Foam
Fabric attached over 1/4″ backer board, w/ 1/2″ fire retardant polyurethane foam, density 2.6 lbs per cubic foot. 6 fasteners per panel min.
Fabric to foam adhesion, custom fabrics
See fabric swatches for standard available fabrics. Specialty fabrics may be available if they conform to our unique formulated 3 in 1 foam adhesion technology.
Typical fabric construction
Marquesa Lana Olefin yarn, 100% solution died, continuous filament Olefin. Shall have 13 fill picks per inch, 13 warp ends per inch, weight 16 Oz per linear yard, including backing.
Fabric fit and installation
Fabric will conform to all corners and edges without exposed folds or creases. Fabric and foam pad will be removable for maintenance or replacement if required. Stiching will not be visible.
Hinge mechanisms & testing
The hinge mechanism shall be certified to pass seat cycle oscillation testing, ASTM designation F851-87 test method for for self rising seat mechanism, and sandbag testing. Testing will require a force of 500 lb load, with over 100000 cycles, without failure of sign of wear.
Fire retardancy
All fabric shall meet or exceed class 1 flammability requirements of the US dept of Commerce, standard 191-53 per bulletin # 117, (California)
Material of back
The seat back will feature the most advanced ergonomic design, allowing the user optimum comfort for lengthy durations, while maximising lower lumbar support, shoulder, back and leg curvatures with proper air ventilation to contact areas.
Material of bottom
Seat bottom construction will have ergonomic and longevity features inherant. The front edge of the cushion will permit proper under leg support, and not “flatten” within 10 years of normal use. Cushion will also have conduits in the surface pad design for air to flow while in use.
Chair bottom and back body
Lightly textured surface, constructed double wall, polyethylene plastic w/anti-static compound, wall.125″, rotational blow molded. Parts will be free of voids, and all edges will clean and smooth, with no exposed air holes.
Paint and plastic
Where applicable, Nema LD3, HGS, (General purpose type, .048″ thickness), will be cut and trimmed for durability and smooth handling.
Type
ASTM test, F89, D1248-78, Value – III
Class
ASTM – D1248-78, Value A
Category
ASTM – D1248-78, Value 5
Melt flow
ASTM – D1238-79F, Value – 10g/10min, 10g/10 min
Density
ASTM – D1505-68, Value – 59.3 lbs/ft3, 0.950g/cm
Mechanical Classification – Tensile strength at yeild
ASTM – D638-77A, Value – 3700 psi, 25 Mpa
MC – Elongation at break
ASTM – D638-77A, Value – 800 %
MC – Tensile modulus of elasticity
ASTM – D638-77A, Value – 120,000 psi, 830 Mpa
MC – Flexural stiffness, Canteleiver beam
ASTM – D747-70, Value – 115,000 psi, 790 Mpa
MC – Tensile impact
ASTM – D1822-79, Value – 125 ft. lbs/in2, 26 joules/cm2
MC – Impact brittleness temperature
ASTM – D746-79, Value – <-105degree F <-76 degree C
MC – Environmental stress crack resistance
ASTM – D1693-70, Value – 450 hrs.
MC – Hardness, Shore D
ASTM – D2240-75, Value – 68
Plastic panels and parts standards
Plastic shall meet or exceed performance standards as defined under N.E.M.A.
Wood
All woods components will be solid finished wood, or plywood featuring a minimum of 10 layers per 1/2″ of wood. All exposed wood will be finished and sanded with sealant, and stained (if required) or laquer as per specification.
Steel pan
Any applicable sheet steel products will be formed or stamped with smooth radius corners. All edges wil be folded and there shall be no exposed drilled or puched openings. All steel pans or parts will be treated, with a baked on protective finish, and be rustproof.
Steel tubular components
Tube will have rounded edges, and all cut areas are to be ground free of burr. Tubing will receive a phosphorization treatment before powdercoated as per specification.
Cast steel components
Casting shall be solid steel, free of voids or seam slag, grit blasted, and pre-treated in iron phosphate wash before paint.
Cast aluminum components
Cast aluminum standard us a 11111 alloy, with a secondar hardening process. Final casting is washed and treated before a baked on powdercoat paint application as per specifications.
All welded connections
All welded connections, will be mig welded with no voids and tack welds. Any weld ground flush will have been V grooved. Welds are to be certifiable under the AWC.
Extruded aluminum components
All aluminum components will be extruded using a 6061 – T6 alloy, or 6351, T6 and be treated to prevent oxidisation, or deterioration. All cut edges will be free of burr, and have no exposed opening greater than .250″.
Padded fabric panel, connection to seat back
All panels will be connected to seat back using rust proof, and oxidization proof fasteneners, and to be hidden from pulic view or access. Fastening system will allow removal of panel if required, without damage. There wil be a minimum of four connection points per panel.
Seat back hardware
All hardware components are to be minimum grade 5, stainless, or zinc plated to prevent rust. All nuts must have nylon insert, and be tightened into lock position.
Seat back testing
The seat back shall be certified to pass seat cycle oscillation testing, ASTM designation F851-87 test method for for self rising seat mechanism, and sandbag testing. Testing will require a force of 500 lb load, with over 100000 cycles, without failure of sign of wear.
Flame testing and certification on fabric
All fabric shall meet or excede class 1 flammability requirments of the US deptof Commerce, standard 191-53 per bulletin # 117, (California)
Flame testing and certification on foam pad
All padding shall meet or exceed class 1 flammability requirements of the US dept of Commerce, resiliant cellular materials, commercial standard 191-53 per bulletin # 117, (California), method 5903.2
Acoustical properties
Seat will conform to acoustical testing as defined ISO 345, meeting sound absorbtion coefficient range of .25 to .51, while subjected to full frequency projection of .27 to .65 Hz.
Abrasion resistance
Tested at 250 lb load at 45 degree force angle, provides a friction force of 16 %
Outdoor durability test results
Test requires exposure to rain & dew. Dew is more damaging than rain because it remains on the material for a long time, allowing significant moisture absorption. A long, hot condensation cycle reproduces the outdoor moisture phenomenon. Test must be accredited to perform ASTM G154 accelerated weathering tests.
UV resistance testing
UV testing requires exposing samples to 42 cycles of 8 hours of UVA-340 ultra-violet light at a temperature of 60C followed by 4 hours of condensation (dew) at 50C for a total of 21 days of exposure.
Plastic flame retardancy
Plastic shall have a maximum burn rate of 6″ per minute as defined in accordance under ASTM D635, or dept of motor vehicle safety standard NO. 302.
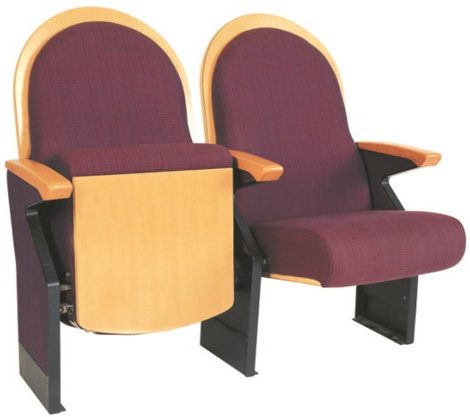